Strengthened by 50 years of prefabrication experience, we are continues to stay ahead of the times by developing advanced technologies -it is number one in acquiring new technologies- designing and producing building components for both housing and industry, for roads, railroads, and large plants.
We are is among the first manufacturers of GFRC (Glass Fiber Reinforced Concrete) in Europe. This material is made of reinforced concrete with AR glass fibres, especially suitable for the construction of lightweight architectural facades. Its lightweight characteristic is one of the most important features of this product, which can take on the most exquisite architectural shapes thanks to its unusual malleability and ductility.
GFRC is therefore an extremely versatile material which allows for extensive architectural design freedom. We are develops GFRC product and medium-heavy finishing product design and manufacture and has been operating for over 40 years in this particularly prestigious market niche, especially in North American and Northern European markets.
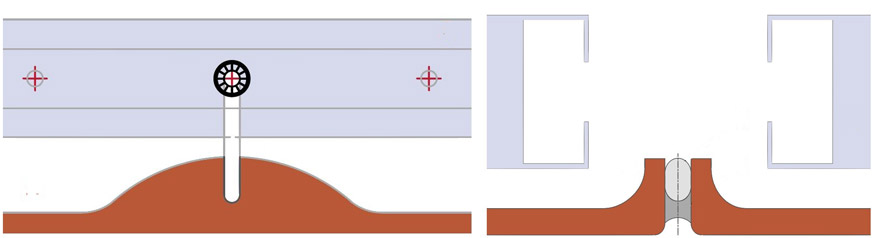
We have contributed to the success of many construction works in Europe and the world through the production of architectural panels for facades and for residential, office and commercial buildings and of raised technical floors.
FEATURES
The technology of the GFRC architectural panel with a metal frame, developed in the USA in the late nineteen-seventies, consists of connecting the GFRC skin to a metal frame during the casting process.
The metal frame connected to the GFRC skin by means of stainless steel elements has the purpose of supporting it and of transferring the stresses and strains that the GFRC front will undergo (force of the wind, own weight, seismic action, etc.) to the structural anchors.
Each of these flexible anchoring devices, which can be likened to genuine plummets, consist of a round stainless steel bar, one side of which is secured to the metal frame by means of the holes in the steel section.
The material known as the patch is wrapped around the nail and welded to the skin over a large connecting surface.
The metal frame is made of cold-formed hot-galvanised sections welded to one another and with provisions for connection to the fixed points on the structure by means of steel brackets.
The shape and size of the frame are established with reference to the specific needs of the project, determined by the architectural configuration, by the conditions of interfacing and support of possible
doors or windows, and by the constraining conditions that can be achieved.
GFRC architectural panels are made in accordance with the technical specifications of the Prestressed Concrete Institute (P.C.I.), in addition to the applicable regulations.
GFRC panels are available in two different thicknesses:
a) 12 mm.
b) 18-20 mm.
Depending on the type of finishing:
a) White or grey concrete surface finished in formworks;
b) White or grey concrete surface with marble grit (from all over Italy) finished with subsequent sanding operations.
This means that many different final finishes can be obtained.
One of the most important methods for making the colour last in time is to use marble grit mixed with cement.
The colour options resulting from natural mixtures without using products other than aggregates, are as many as there are possible combinations between the many different aggregates available
on the market.
PRODUCTION
The panels are manufactured according to a daily cycle.
Production is made up of the following stages:
1) Creation of the outer surface of the panel using formworks designed specifically in relation to the project.
2) Application of the first marble grit surface and of a subsequent layer of GFRC for a thickness of about 12 mm.
3) Connection of the mechanical frame to the GFRC skin.
4) Curing of the artefact for about 24 hours.
5) Removal of the artefact from its mould.
6) Seasoning of the artefact for a period of about 7 days.
7) Sanding and finishing.
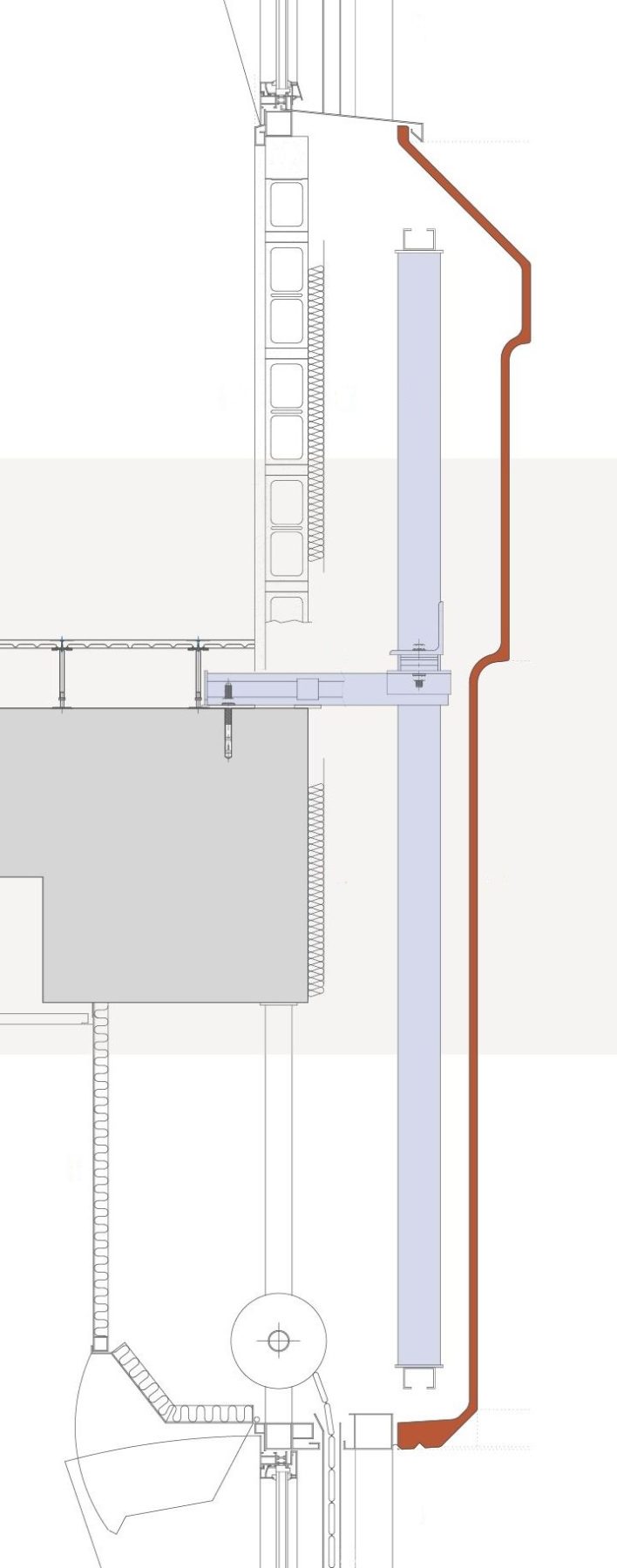
OUR LAST PROJECTS

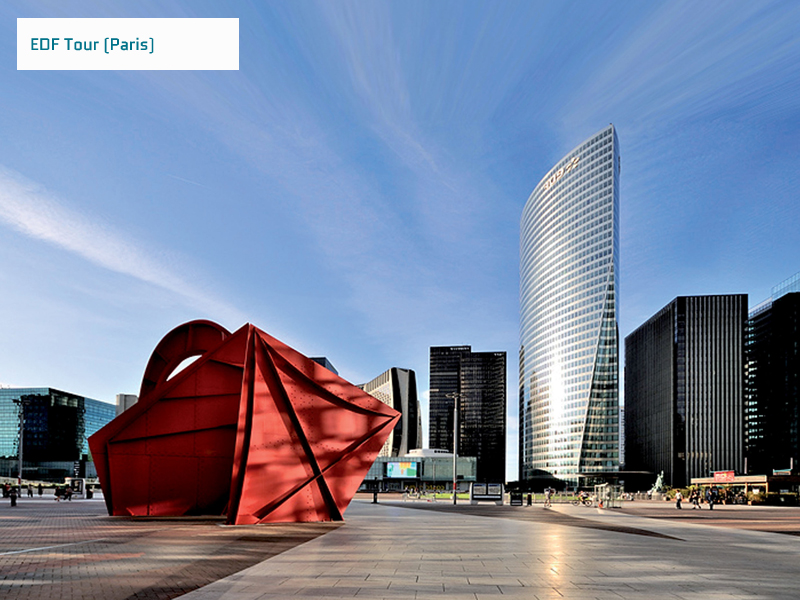
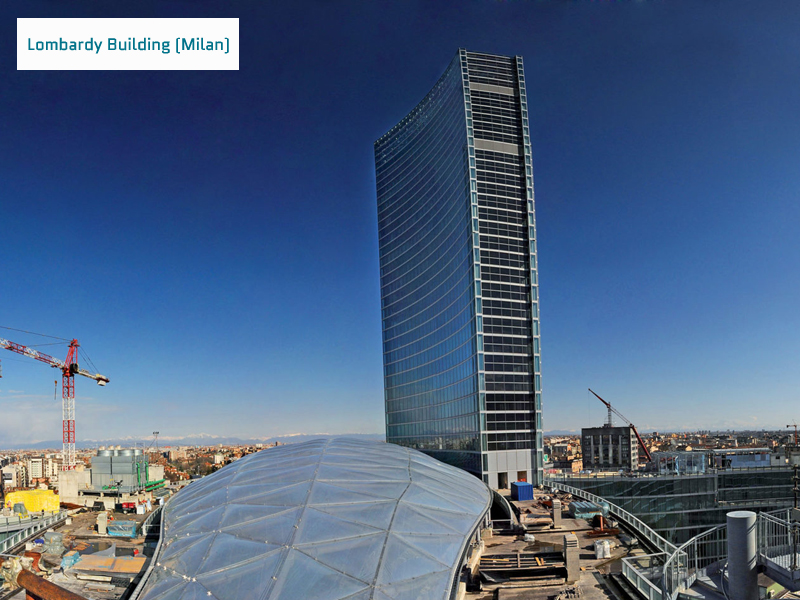
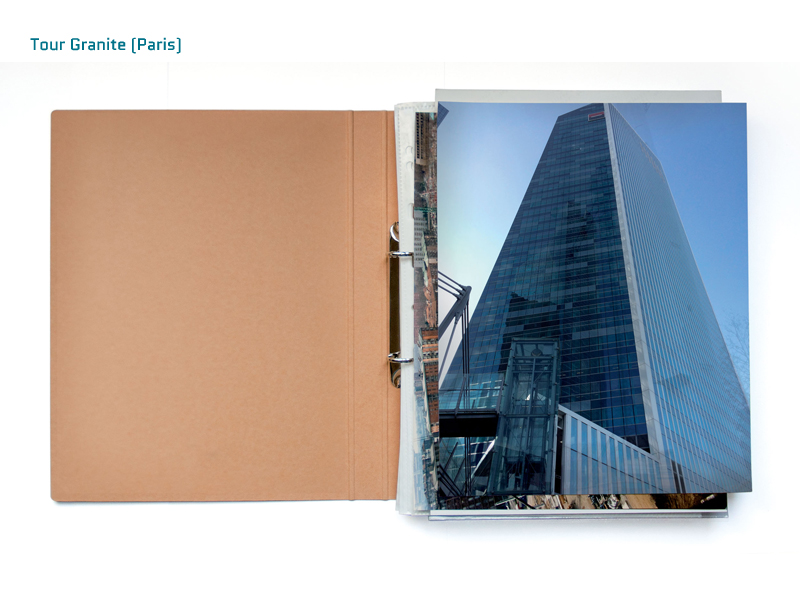